
Dust Collector Purchase Guide
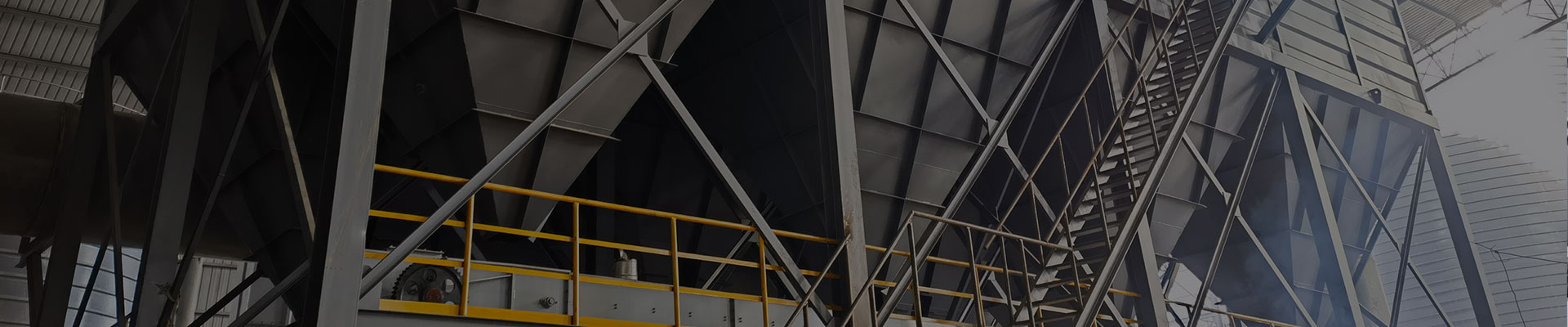
Customized Service Process

Determine Handling

Determine
Filter Area

Select Appropriate Filter Bag Material

Procure Auxiliary Components

Choose Disassembly & Maintenance Scheme
Key Considerations for Industrial Dust Collector Selection
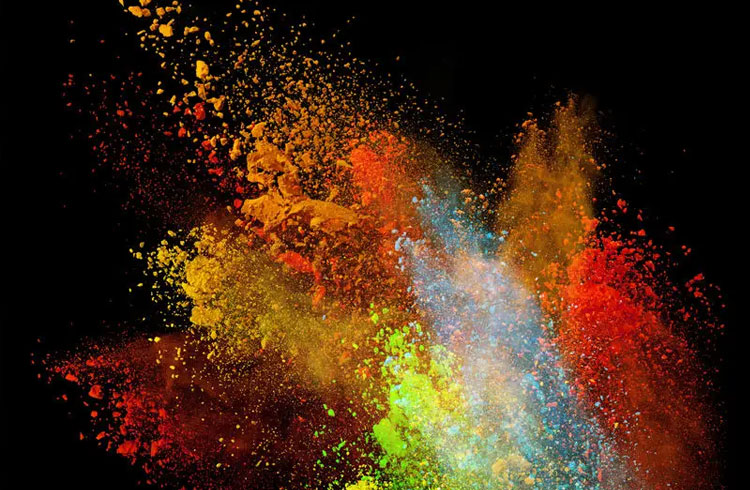

Dust Properties
Essential Dust Properties for Collector Design:
1. Particle Size – Defines filter porosity and efficiency thresholds
2. Bulk Density – Affects settling dynamics and pneumatic transport needs
3. Chemical Reactivity – Determines material compatibility (corrosive/abrasive risks)
4. Temperature – Sets thermal stability limits for filters and seals
5. Moisture/Oil Content – Influences dust agglomeration and filter permeability

Calculating Airflow
CFM Definition & Function – Cubic Feet per Minute quantifies air volume extraction capacity, directly impacting dust-laden airflow dynamics within industrial environments.
System Design Optimization – Undersized CFM risks non-compliance with air quality standards; oversized CFM escalates operational costs and process instability.
Rationale: Aligns with engineering principles for pneumatic conveyance and system design standards, emphasizing CFM as a core metric for performance and regulatory adherence.
Key Factor 1 & 2:
1.Precise CFM (cubic feet per minute) alignment ensures optimal dust capture efficiency.
2.Dust Collection Mechanism: Capture method (hood, duct, etc.) impacts airflow dynamics.
Key Factor 1 & 2:
3.Duct Diameter: Directly influences velocity and pressure drop
4.Workspace Volume: Total cubic feet requiring ventilation
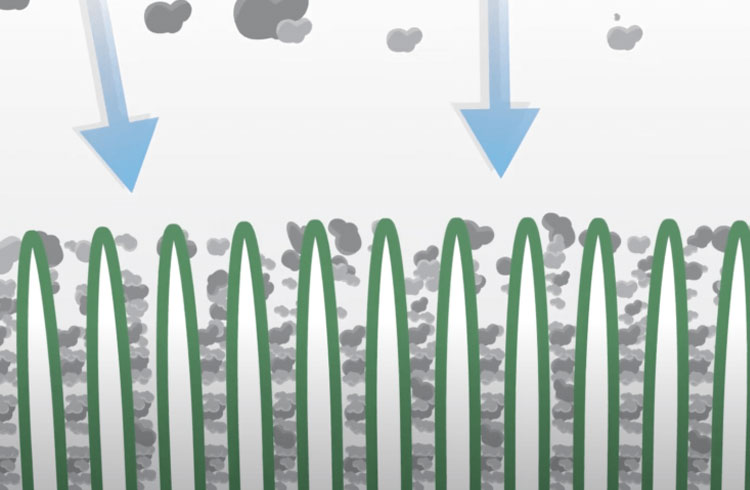

Air-to-Cloth Ratio Determination
Calculation of gas volumetric flow per unit fabric area to balance filtration efficiency, energy consumption, and filter longevity.
Total Filtration Area Calculation
Divide system air volume (m³/h) by the air-to-cloth ratio (ACR) to derive required filtration area.
Filter Cartridge Quantification
Determine filter count by dividing total filtration area by individual filter media area.
Model Selection Criteria
Match filter cartridge quantity and collector type (e.g., baghouse, cartridge) to application-specific operational requirements.

Choose Right Type of Pulse Jet Dust Collector
1.Pulse-Jet Baghouse
Advantages: Continuous cleaning during operation; Low maintenance costs; Flexible sizing.
Limitations: Requires compressed air; Unsuitable for high-moisture (>20% RH) applications; Mandatory filter cages.
2.Reverse-Air Baghouse
Advantages: Gentle cleaning prolongs bag life; Modular design for partial maintenance.
Limitations: Frequent cleaning required; Higher bag costs vs. pulse-jet; Customized bag fabrication delays.
3.Shaker Baghouse
Advantages: Simple operation; Low upfront investment.
Limitations: Limited media options; Large footprint; Inefficient for high dust loads.
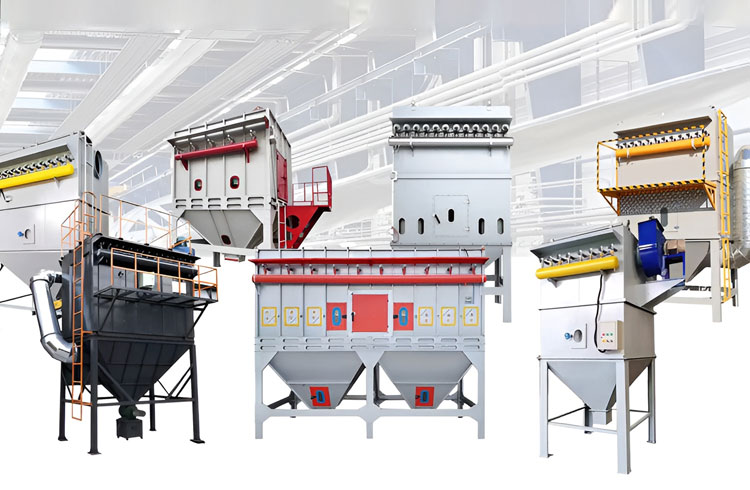
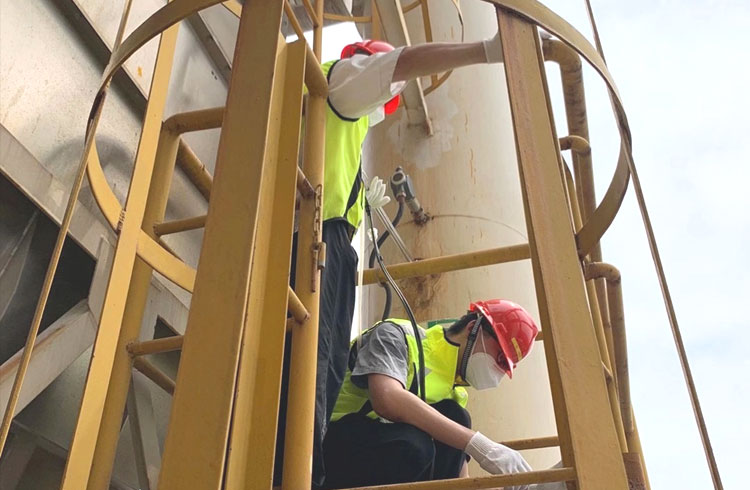

Choose Low-Maintenance Dust Collector
Implement low-maintenance protocols and energy-efficient solutions to reduce recurring operational expenditures .
Reason 1 for Selection
Ensures reliable operational performance, minimizes mechanical wear, and extends equipment lifespan through adaptive cleaning cycles.
Reason 2 for Selection
Facilitates seamless system expansion, maintenance accessibility, and space-efficient integration via standardized, scalable components.
Reason 3 for Selection
Enables rapid (<30-minute), tool-free filter replacements on the clean-air side, supported by universal filter sizes and application-specific configurations to ensure cost-efficiency and operational continuity.
Please send your message to us
- *Tel
- *Title
- *Content